Comparatif entre le fonctionnement continu et batch et leur influence sur la consommation énergétique
Ces 2 types de fonctionnement existent en industrie.
Un process en fonctionnement continu est caractérisé par une alimentation en matières « en continu ».
Cette matière subit alors différentes étapes de transformation et elle est pour cela généralement transportée au sein de l’équipement passer pour passer au travers de ces différentes étapes, et finalement sortir de l’équipement après transformation.
Un process continu est un système ouvert.
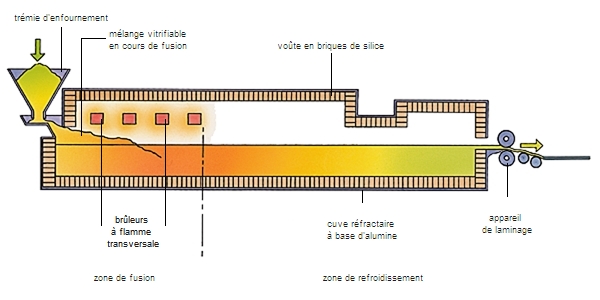
Four de production de verre – Larousse en ligne
Un process en batch est lui un process discontinu. L’alimentation en matières se fait à un moment donné, pendant un certain temps permettant au maximum de « remplir » l’équipement. L’entrée est ensuite fermée et la transformation démarre.
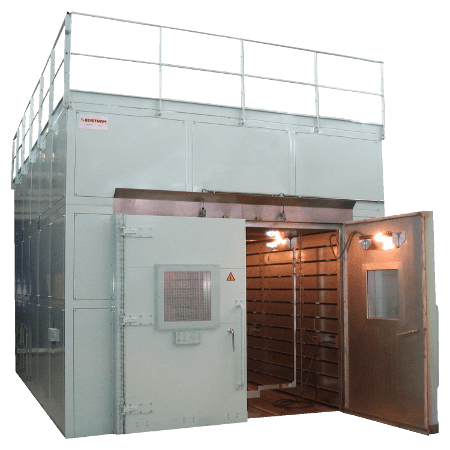
Four batch – Elmetherm
La matière peut subir différentes étapes de transformation l’une après l’autre mais ces étapes se déroulent l’une après l’autre au même endroit, sans déplacement de matières.
Lorsque la transformation souhaitée est terminée, le produit est en est extrait.
Et on pourra redémarrer un nouveau « batch » par la suite dans cet équipement.
Un process en batch est un système fermé.
Pour différents types d’équipements…
Les fours sont un de ces équipements conçu soit pour du travail en continu, soit en batch.
Les fours continus (appelés aussi fours tunnels) sont par exemple des fours à rouleaux, à tapis, à wagons…
Les fours batch peuvent être des fours à sole mobile, fixe ou élévatrice ou des fours à cloche par exemple.
Les réacteurs ou cuves sont un autre exemple d’équipements pouvant travailler en continu ou en batch.
Les avantages et inconvénients du fonctionnement en batch
L’avantage ici est qu’il est possible d’utiliser cet équipement facilement pour différentes matières/produits à travailler.
On réalise certains batchs pour tel produit puis d’autres batchs pour un autre produit etc.
Pour chaque produit, on réadapte les paramètres de fonctionnement (également aussi au niveau des besoins de chaud/et ou froid) du process. On peut donc utiliser un même équipement pour la production d’un grand nombre de produits différents.
Chaque nouveau batch offre la possibilité de changer les paramètres du process parfois de manière très significative.
Le gros avantage est donc sa flexibilité.
Le réglages des paramètres de fonctionnement d’un batch à l’autre implique une surveillance de fonctionnement accrue.
De plus, la qualité du produit peut se retrouver dès lors légèrement différente d’un batch à l’autre. Le rendement de production est certainement moins bon.
Ce type de process est adapté pour des volumes de production plus petits et lorsqu’il y a beaucoup de variétés de produits.
Le démarrage de l’équipement nécessite une phase de lancement (pré chauffage, ) et des étapes post production (nettoyage,...) qui sont une charge économique et environnementale portée par la production d’un lot. Plus le lot est petit et plus le ratio de ces charges est élevé.
Les avantages et inconvénients du fonctionnement du continu
Le gros avantage du fonctionnement en continu est qu’il engendre des économies d’échelle : pour un même volume produit, la consommation d’énergie et le besoin en main d’œuvre est nettement moindre.
Une fois ici les paramètres de fonctionnement réglé, on n’y touche plus pendant un certain temps.
La qualité du produit est donc également plus stable.
Il est donc adapté lorsque les volumes de production d’un même produit sont importants.
Son inconvénient majeur est son manque de flexibilité.
Il n’est possible d’optimiser le process que via du “fine tuning” et des erreurs de paramétrage conduisent à la production de produit non qualifié.
On peut ainsi noter que si, malheureusement, les volumes de production baissent à cause du marché, ses avantages s’en trouveront réduits. L’idéal est évidemment que ce process en continu fonctionne au maximum de sa capacité pour pouvoir en tirer le meilleur rendement.
Ce qui est évidemment une grosse exigence pour l’utilisation des ressources humaines.
Le démarrage d’un processus en continu génère généralement des premiers produits non conformes qui doivent être jetés ou recyclés.
Un dysfonctionnement à une étape de la production peut perturber l’ensemble de la ligne et créer des produits non conformes.
L’approvisionnement et le stockage doivent pouvoir suivre le fonctionnement de la ligne.
La consommation énergétique par produit est diminué MAIS à la condition que les lignes soit exploitées significativement.
Des autres systèmes...
Bien sûr il existe des systèmes qui sont intermédiaires.
Le choix du bon système de production intègre de nombreux paramètres, mais ce questionnement doit systématiquement être fait. Il n’est pas rare de voir des systèmes de production qui sont de simple “copier/coller” de modèles existant depuis plusieurs décennies alors que les données ont changé.
RÉSERVEZ UN APPEL GRATUIT POUR DISCUTER DE VOTRE PROBLÉMATIQUE...
Uniquement via réservation sur agenda (sous réserve de disponibilités).